While the world hopes for a positive path out of the pandemic, recent history has taught us not to let down our guard. The last 18 months have been a rollercoaster ride for every company, unsure about when the next supply chain crisis or staff shortage will hit and cause acute disruption to business. In this sea of uncertainty, companies need any edge they can get to help them to build resilience into their operating model.
In recent years, owner-operators (companies who invest, engineer, operate, or maintain an asset intensive facility) have benefitted from the growth in sensor and IoT technology, which has provided unprecedented insights into every corner of their businesses. Stakeholders can now measure how their assets are performing at any time. While this has undoubtedly revolutionised industry, this technology needs to evolve to the next stage if producers are to overcome the seemingly endless obstacles ahead.
Fortunately, solutions to these challenges are coming to light. By combining artificial intelligence (AI) with traditional Asset Performance Management (APM) programs, owner-operators can benefit from a new era in smart automation – APM 4.0, which does more than just monitor the current situation. Rather, using predictive analytics, APM 4.0 is able to foresee future crises and trigger “just-in-time” reactions, preventing unnecessary unplanned downtime and a rise in maintenance costs.
However, while revolutionary, APM 4.0 is not a panacea. It requires a careful and well-planned approach if it is to be effective.
Establishing a strong data management strategy within manufacturing
Upgrading Industry 4.0
Automation and information are the themes of the decade, with mechanical devices increasingly being replaced by electronic components in manufacturing, industrial, and factory environments. The flourishing data ecosystem in factories and warehouses, fed by numerous sensors and processed into insights in the cloud, have offered owner-operators greater visibility into bottlenecks, potential efficiency gains and other important aspects of production. However, while insights into real-time data are obviously highly valuable, they are outshone by the potential to predict the future of production.
This is where asset management becomes intelligent. The data gathered by the sensors can be used by AI to predict the future behaviour of equipment, allowing technicians to plan maintenance and production in far greater detail and with greater confidence than ever before. While it is inevitable that all assets will eventually need downtime for repairs or upgrades, knowing when this will be with a high degree of accuracy allows owner-operators to minimise shutdowns while mitigating risk and optimising efficiency.
Even the best tools need proper handling
While APM 4.0 is clearly a powerful lever, owner-operators must have a carefully planned approach to realise the full value. Rather than being a self-contained, plug-and-forget solution, predictive analytics should become one part of a well-designed asset performance management strategy.
In order to realise this, alerts need to be prescribed using four elements to help categorise their priority and the action needed:
- Criticality: What is the financial impact of this predicted failure? Impact is the total effect of the event if the predicted failure mode occurs.
- Urgency: How much time do you have? Urgency is a reliable prediction of when the failure mode will occur once the indicator alarm is triggered.
- Action: What action will you take? It defines the tasks you need to execute and includes the required skills, tools, permits, work instructions, and required asset safety isolation.
Funneling every alert from the APM 4.0 program through these steps allows the operator to act on important lead indicators without becoming overwhelmed or reducing asset performance. As such, the value of both the assets and the APM 4.0 solution are maximised.
Climbing to new heights with the aid of real-time data analytics
The right tool for the job
An effective APM 4.0 strategy connects engineering, operations, and performance. It lays the foundation for successful, streamlined digital transformation by establishing an easy-to-understand framework including best practices, integrated system solutions, and single truth data models. It provides an actionable, evidence-based roadmap that prioritises improvement in tasks and investments while aligning business objectives.
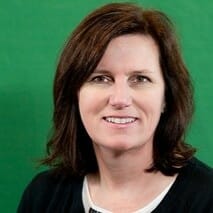