Following the recent introduction of the UK Building Safety Bill, Antony Brophy, UK director of business development at Cobuilder, discusses why standardised data is essential for the construction sector
Last month marked an important milestone for the construction industry, as the Building Safety Bill received Royal Assent from UK parliament. The Bill, which was drawn up in the wake of the 2017 Grenfell Tower fire, has been put in place with the aim of enhancing regulation around building safety and construction.
Now, five years after the horrors of Grenfell, the Bill is likely to have a big impact on all areas of the industry by widening liability for building owners, developers and product manufacturers. Significantly, the Bill will introduce the requirement for a ‘golden thread’ of information to be set up before work on a building begins and kept updated throughout the design and construction process.
The intention of this is to ensure traceability, so that anyone working on the building can easily access reliable and up to date information about which materials are being bought and used, and how these have been installed – at any point of the process. It’s therefore key that processes are put in place to make information easier to manage.
Where existing problems lie
The construction industry, however, is facing several barriers that are preventing a standardisation of information from becoming more widespread. Not only are these barriers hampering how efficiently data is able to be collected, but they are likely to impact businesses’ abilities to adhere to the Building Safety Bill’s requirements.
Traditionally, information about products has proven difficult to gather in one place. When delivering products to a construction company, manufacturers will often share product data in a range of sources and formats. They may, for example, deliver a PDF document made up of hundreds of pages detailing product specifications. It can take a constructor a huge amount of time to pick through this to find what they need.
On top of this, many construction companies are still dealing with paper-based processes, which leaves information in silos and slows down their ability to draw on insights. This is further complicated by the fact that multiple actors are involved in the design and planning of a building, which can make it a challenge for one person to take ownership of data management.
The opportunity that data presents
Data presents a huge opportunity for those companies that are willing and ready to harness it. With multiple stakeholders involved in construction projects, it has the potential to facilitate decision-making, serving the needs of everyone from manufacturers through to contractors and subcontractors.
When it comes to gaining oversight of products used in the construction process, improving data management also enables better traceability – everyone can see where a product came from and what it can be used for. This can give project managers and procurement teams a clear footprint for what they are buying and selling.
Equally, structured and accurate data matters even more for businesses today from a sustainability perspective. The UK built environment is currently responsible for 25% of total UK greenhouse gas emissions, and national steps are being taken to address this, with the government outlining a performance-based policy framework for energy use in large commercial and industrial buildings. Constructors need to be able to understand the environmental performance of products and assess the environmental impact that a construction project might have, so businesses can meet their sustainability objectives.
Ultimately, who owns the data is key – but by finding a centralised point of reference for it, everyone can take ownership at different stages of a project.
Finding common ground
Many construction companies have progressed with digitising the way they work. For example, the usage of BIM standards, to organise and digitise information about buildings, has been rising in recent years in the UK. However, data quality management still needs to be better understood, as it is a vital part of ensuring that any data gathered remains accurate and reliable.
Being able to provide product information that is both machine-readable and consistent is key to making data management a seamless process. By structuring it in the format of common data templates, organisations can find a single digital language that improves the way they exchange information on products, materials and components throughout a building’s life cycle. Everyone involved in a construction project – from the manufacturer to the end-user – can then understand how and where information is held.
This method of structuring and transforming data should be implemented across the construction industry, as it will enable organisations to bring forward their digitisation initiatives and facilitate data exchange. Most crucially for UK businesses, it will help them to achieve the ‘golden thread’ that forms an essential part of the government’s Building Safety Bill and ensure that the likes of Grenfell never happen again. The construction industry needs to start thinking globally and acting locally. We need ‘competent’ people doing the ‘right things’ and everyone providing evidence of such.
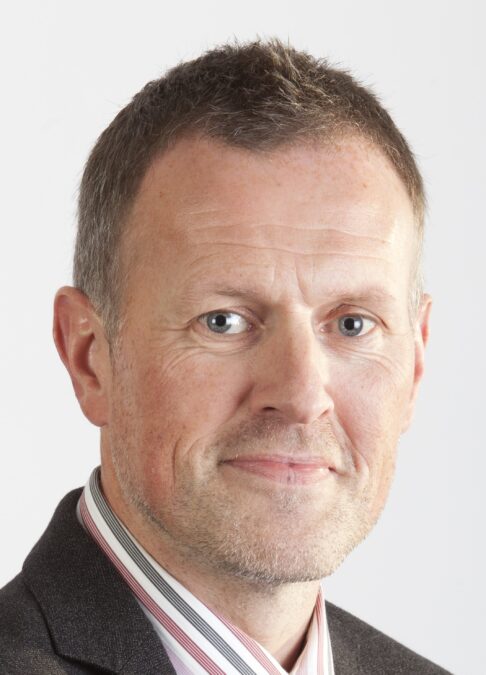